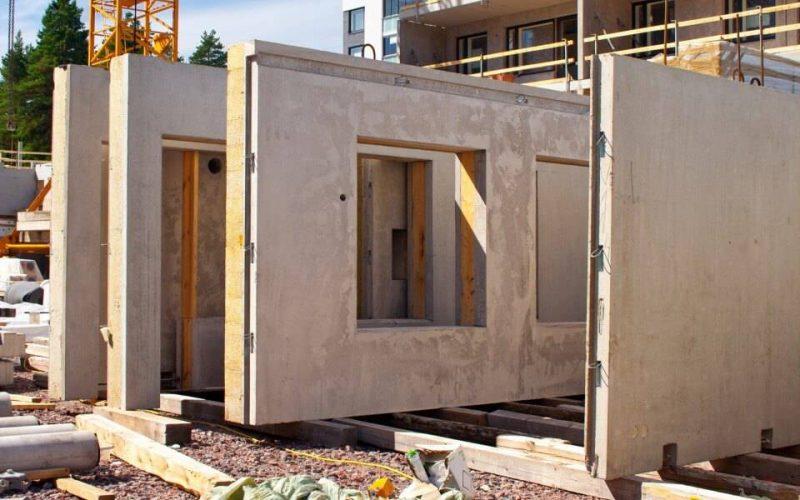
January 20, 2022
Precast concrete Tanks is cast and cured before being transported to a job site, unlike poured concrete, which is poured and cured on-site. The blocks or pavers closely resemble the look of natural stone thanks to the use of fine aggregate, making them ideal for customers who want to enjoy the beauty of natural stone without spending a fortune.
Other applications include storm drains, cattle feed bunks, bridge systems, water tanks, and hazardous material containment. Concrete has grown in popularity to the point where you can find at least one structure or component made of it in any village, town, or city.
The strength of precast concrete is one of its most significant advantages. It’s tough, dense, and impervious to many of the problems that wood and metal suffer from. It doesn’t rot, rust, or corrode, and it maintains its strength for many years. Only if it isn’t laid properly or is subjected to tremendous force, such as during earthquakes, will it cause problems. As a result, it’s a popular choice among today’s consumers who don’t want or can’t afford to deal with high maintenance costs.
Precast concrete, when properly installed, can provide a high level of safety. Because of its high density, it is resistant to damage from heavy impact and can thus be used safely in structures that see a lot of abuse or activity, such as stadiums, apartments, fencing, and walls. Bridge piers, conveyance systems, and waste water management solutions are among the other structures that benefit.
Though there have been some concerns that concrete contains toxic substances, increased awareness and changing trends have resulted in the removal of many harmful additives. Airborne particulates can cause health problems only during the production and construction stages of concrete; once it has been cured, it is safe.
Building monitoring is an important part of maintenance, especially if the building is used for high-stress activities or is built in sensitive areas such as earthquake-prone zones. Precast concrete, which can be fitted with microchips that log data for later analysis, can make the process easier. Engineers can determine how much movement and stress a structure has in order to determine if it needs to be re-strengthened, repaired, or otherwise.
Chemical resistance: Oil and fuel can corrode metal and cause wood to rot. Precast concrete, on the other hand, is impervious to the harmful effects of certain chemicals. This is why it’s used to pave roads and driveways where there’s a lot of oil and fuel spillage but no problems.
The ability of structures to absorb impacts must be high, and the higher the number, the better. Concrete has few drawbacks, making it ideal for use as a perimeter fence or in industrial applications where the ability to withstand heavy loads is required.
Precast concrete is dense and heavy in most cases, but the concrete mix can include other extremely strong materials that allow it to be used finely. Steel fibre reinforcement and carbon composite grids, for example, allow it to be used in more ambitious projects with finer aesthetics. It can also be moulded into creative shapes that follow design trends and are functional.
There are a slew of other advantages to precast concrete, and we only have to look around to see how many applications it serves.
Precast concrete is extremely durable, versatile and strong, possessing a wide range of applications and is resistant to a lot of problems that regular metals face. For an insight into the benefits of precast concrete, browse this link.
Related Items: Precast ConcreteWaste Water Management Solutions