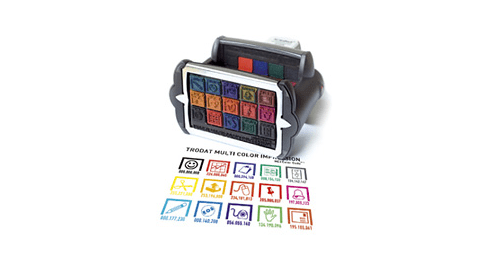
The legitimacy of business documents is certified using the essential article self inking rubber stamps; they play a significant role in commerce and authorizing the document. They are now increasingly used in crafts and Art. The wooden stamps mounted on rubber include the earliest rubber stamps. One came with an ink pad packaged with them.
Therefore, before pressing the rubber lettering onto the paper, one had to push it into the ink pad. These classic stamps were reasonably priced. But the images they produced were blotchy, with some light and some dark. The self-inking stamp is the newest item on the shelf. It doesn’t require a separate ink pad, as the ink is infused into the rubber die.
How Is The Self-Inking Stamp Differentiated?
Self-inking stamps are distinguished by having a separate die and re-inking pad built into a handy spring-loaded mount. The impression of the stamp is created by applying pressure to the mount’s top. When stamping, the stamp die moves from the pad and descends onto the surface to be marked. Self-inking stamps are priced on average, costing more than regular stamps but less than pre-inked stamps.
Self-ink stamp prices are based on the mount size and line count. There are typically six sizes for self-ink mounts. On these self inking rubber stamps, caution should be exercised to avoid excessive pressure or banging. The area that needs to be stamped should be firmly and evenly stamped with the seals. Self-ink stamps have made it possible to print consistently.
How Do The Self-Inking Rubber Stamps Work?
The self-inking stamps typically have three components: the stamp itself, the stamp pad and a housing unit for the two, which also acts as the handle. To use the stamps, one needs to place them on the paper where one wants the image/text to appear. A slight application of pressure depresses the handle half an inch or so. During this movement, the rubber stamp gets inked, and the image appears on paper after the stamp and pad have rotated away. The most useful purchase an enterprise can make is to buy custom rubber stamps as it lessens the human labour on repetitive work.
How Have Rubber Stamps Over The Years Evolved Into Self-Inking Stamps?
For hundreds of years, rubber stamps have been in use. Modern stamps are made of plastic and other sturdy materials and are available in a range of sizes, as opposed to older stamps, which were typically made of wood and rubber and had a limited size range. Some of them also feature “light burst technology” and distinctive laser-engraved spongy rubber material, which can produce almost 50,000 impressions before needing to be re-ink.
Rubber stamping started becoming a common way to mark manufactured products and packages. Stamping companies gained more and more steam through the Industrial Revolution and even more through the World Wars. However, it was in the 1970s that the rubber stamping industry took off, with corporations using them for their correspondence and when people took up stamping as an artistic hobby.
These self-inking rubber stamps are little practical devices with a custom rubber die plate with your text or images. They are self-inking, so unlike the older conventional wood rubber stampers, there is never a need for any messy ink pads. These top-notch stampers have an endless capacity for impressions and have become a necessary article in today’s business world.
Conclusion
The benefit of using such a stamp is that one need not carry separate ink pads; neither does one have to keep checking whether the stamp has sufficient ink. Additionally, self-inking seals produce the same pattern every time they are used and can be custom designed to suit various applications.
Stamp Store provides multiple designed and customised self-inking stamps to make your work feasible and faster. For more details contact us now.