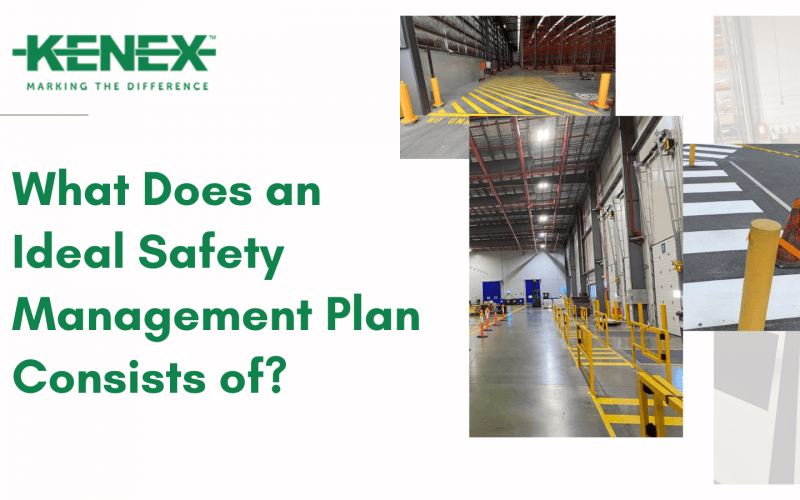
For your workplace or commercial property, the need for a safety management plan is not news. However, even after knowing this, a lot of organizations and property owners fail to implement a well-designed safety plan and understandably so. A safety management plan isn’t something that you can just plan and execute in a day. There are a lot of factors that play a significant role in ensuring that the plan created works out effectively.
This is why whether it is your workplace traffic management plan or safety management plan, you must carry out research first. Research on what does your management plan need for it to be perfect. Prioritizing the employee’s safety is the responsibility of every business owner. With a well-strategized safety plan, you can ensure the employee’s security as well as your property’s.
Here, to help you out, we will discuss some of the major aspects of an ideal safety management plan. By going through these, you will find it much easier to establish a safety plan of your own.
- Safety Norms and Policies
To form an effective safety management plan, the first step is to focus on the safety standards set by your company. Legally setting up safety policies that highlight the major safety concerns is important to let employees know about the possible health risk and how to handle if any of these safety concerns tend to rise. Safety policies include all the documented guidelines that every employee is needed to follow.
Your full-fledged safety standards must cover up every small or big safety-related directions. From instruction on operating different machinery to what to do in case of fire or other emergencies, it should have everything. And in the case of a traffic management plan, including your warehouse line marking is also very crucial.
- Comprehensive Training and Induction
Once the paperwork for safety norms and regulations are done, make sure that regular safety drills are conducted. For something like this, you cannot just be ready on paper. If you have a warehouse where the chances of a certain safety risk are more, you have to practically prepare the workers. These drills shouldn’t just be conducted for the sake of it. Make sure that everyone participates and take the drill seriously.
As far as the frequency of this training is concerned, it must be done after at least every 2-3 months. So that if you have some new employees or a new employee in the team, they can familiarize themselves with the induction program too and be prepared like everyone else. A quality training program is what differentiates a good company from others.
- Safety and Health-Related Talks
Further, higher authorities must communicate safety policies and their importance to the employees. Any decent organization understands that creating and letting safety policies hang in the air isn’t enough. Employees must be personally connected to the plan and told that safety is always the top priority at your firm that also gives them a sense of comfort and reassurance.
If not too often, then once in a while a meeting must be held with the employees discussing the safety norms. You must also take questions and suggestions from the workers on the safety management plan and how it could be made better. Encourage the idea of prioritizing safety, not just of ourselves but our fellow employees result in fewer accidents and also improved productivity.
- Constant Monitoring and Supervision
No matter how perfect you think your safety or warehouse traffic management plan is, you should always look for more errors and ways to enhance it. This way you allow yourself to be on the top of safety plans and prevent more dangers than you think. With time, different safety threats may come up, if you create a safety program once and leave it to be, you are making a mistake.
You should give a fair amount of time and effort to keeping an eye on the safety policies and how they are working out for you. With constant monitoring, you also let the employees know that these must be followed with utter seriousness. To reduce the chances of risks, a high level of supervision is a must.
- Reporting Safety Concerns
Ensuring work safety is not just a task that you can assign to your employees. It is a work ethic, a work culture. As a business owner, your job is to make it known to the workers that there is no shortcut when it comes to safety. Therefore, you must encourage them to report any small or big safety issue that occurs anytime.
They should be given a sense of responsibility for it. For example, in case the warehouse line marking at some areas are faded, they should ask for it to be repainted immediately. If each employee starts to notice and talk about safety, the entire workplace’s safety enhances automatically.
Hire Professionals for your Safety Management Plan
Once you are aware of what your safety management plan should include, you have a different challenge to face. Hiring experts to help with your safety management plan. In case, you are looking for one right now, here’s what you should consider:
- They must be experienced in the industry so that they know what possible problems could emerge and can also deal with them effectively.
- They must be a well-established firm with expert professionals so that you can rely on them and can trust their services.
- Along with the safety plan, they should have other similar services like traffic management plan to offer as well.
Conclusion
The information given above is all you need to make sure you successfully get your safety management plan ready. And the sooner you get it, the better because safety isn’t something to play with. And if you haven’t been able to find a reliable company to help you with the same, visit Kenex Stencils. They are trustworthy and experienced service providers for line marking, safety management plan, and more. You can seek their professional expertise for your workplace’s safety management plan anytime.